1000
Asia Pacific J Clin Nutr (1997) 6(2): 92-94
Asia Pacific J Clin
Nutr (1997) 6(2): 92-94

Dry
mixing technique for the large scale production
of iodine fortified salt in India
S Ranganathan1, S Sundaresan2,
I Raghavendra3 and S Kalyani3
1National Institute
of Nutrition, Indian Council of Medical Research, Hyderabad, 2Salt
Department, Government of India, Jaipur, 3Department
of Industries and Commerce, Government of Tamilnadu, Madras
Dry mixing technique was used successfully in three
factories in India for the manufacture of iodine fortified salt.
Permitted food additives, calcium carbonate and magnesium carbonate,
were used with potassium iodate. The technology was smooth and free
from any problem. Since the formerly conventional, but now superceded
on analytical performance criteria, spray-mixing system was not
used in the study, plants of the economics either batch mixing or
continuous processes were more in evidence, and could be compared
with avoidable spray mixing production performance data. The iodine
fortified salt was free-flowing and retained the colour of the common
salt. The iodine distribution was uniform (about 30 ppm). Long distance
road transportation did not affect the iodine stability and its
consistency. Storage studies showed satisfactory stability and the
fortified salt had prolonged shelf-life beyond one year.
Key words: Iodine fortified salt,
potassium iodate, calcium carbonate, dry mixing, free-flowing, stability,
shelf-life, India, Tuticorin, Machilipatnam, Hyderabad
Introduction
Iodine deficiency disorders (IDD) constitute a major
public health problem in India which afflicts millions of people.
Available evidence reveals that no state in the country is free from
IDD and population studies, whenever undertaken, are continuously
exposing new pockets of iodine deficiency1. It is estimated
that nearly 167 million people are suffering from IDD of which 54
million have goitre. 2.2 million are cretins and 0.6 million have
mild neurological problems2. Fortification of common salt
with iodine is a long term and sustainable low cost approach to control
IDD as this will enable the population to ingest daily the required
amount of iodine3. The reasons are clear: salt is one of
the few food items which is consumed universally irrespective of socio-economic
status, salt fortification with an iodine compound is a simple mixing
operation without any chemical reaction, the colour, taste or flavour
of the fortified salt are the same as that of the common salt, and
it is acceptable to all since no change is observed in the organoleptic
properties of foods prepared from iodine fortified salt.
The technology of salt fortification with iodine is
well established in India. The usefulness of the dry mixin 1000 g
technique, when compared to conventional spray mixing, in increasing
the stability and shelf-life of iodine fortified salt has been clearly
demonstrated by laboratory studies in India4. However,
infor-mation on the large scale production of iodine fortified salt
by dry mixing technique in India is scanty. It was recommended in
the "Motivation Campaign on IDD control through Salt Iodation",
to explore the possibility of a pilot plant and also the feasibility
of converting the existing spray mixing plants to dry mixing plants
with minimum financial liability5. Therefore, studies were
under-taken in three factories in India to manufacture iodine fortified
salt by the dry mixing technique.
Methods
Studies were conducted in three factories in India.
They were: M/s. Sahayamatha Salterns (P) Ltd, Tuticorin (Factory A).
M/s. Laahar Salt and Chemical Works (P) Ltd, Machilipatnam (Factory
B) and M/s. Jaybharathi Salts (P) Ltd, Hyderabad (Factory C).
Factory
A
Edible grade solar crystal salt from Tuticorin was
powdered and used. Food grade potassium iodate (KIO3),
dissolved in a minimum volume of water, was mixed with powder salt
in a 100 kg stainless steel ribbon blender. After thorough mixing
for ten minutes, the salt iodate-mix was dried. This had a KIO3
equivalent to 6000 ppm iodine. Iodine fortified salt was prepared
by dry mixing, for five minutes, the required quantity of the salt-iodate
mix and powder salt in a 250 kg stainless steel ribbon blender. Light
basic magnesium carbonate (0.3%) was added as a stabiliser/ anticaking
agent. After completing the fortification, the iodine fortified salts
from different regions were tested by the field kit6 for
iodine content and uniformity on the spot. Representative samples
were tested by the titrimetric method7 in the laboratory
of the factory. Samples were also drawn for testing at the Salt Department
laboratory, Government of India, Tuitcorin, India; Tamil Nadu State
Government Laboratory, Madras, India; and the National Institute of
Nutrition (NIN), Indian Council of Medical Research, Hyderabad, India.
Trials were also done in the same manner using crystal salt and salt-iodate
mix to produce iodine fortified crystal salt.
In order to study the effect of transportation on
the stability and distribution of iodine in the fortified salt, samples
were sent in a 50 kg high density polyethylene (HDPE) oven sac by
road transport to the NIN where the iodine content was tested by the
titrimetric method7. Also, the stability and shelf-life
of the iodine fortified salt, when stored at ambient temperatures,
were studied every month for one year.
Factory
B
Batch mixing process: Edible grade crystal salt from Tuticorin was crushed and used. One part
of food grade potassium iodate was mixed well with ten parts of food
grade calcium carbonate and the mix was added to 500 kg crushed salt
taken in the ribbon blender in which the spraying system was disconnected
and not used. The level of iodation was 30 ppm. After thorough mixing
for ten minutes, the fortified salt from different regions were tested
for iodine content on the spot and also by the titrimetric method
as in Factory A.
Continuous process: The spray mixing plant (similar to the Sambhar model) which had been
used for salt iodation in the factory was available for the dry mixing
technique. The roller crusher, belt conveyor and the worm-screw mixer
were put into use and the spraying unit w 1000 as not used. In the
dry mixing technique, 25 kg crystal salt was loaded into the roller
crusher followed by the addition of iodate-carbonate mix (potassium
iodate 1.25g and calcium carbonate 12.5g) to give an iodine content
of 30 ppm. Then another 25 kg of salt and iodate-carbonate mix were
added and the same addition cycle was repeated continuously. After
crushing, salt and iodate-carbonate mix passed through the conveyor
belt and fell into the worm-screw mixer for final mixing. At the end,
iodine fortified salt was collected in bags. The iodine content, its
distribution, spot test, titrimetric estimation, the effect of transportation
and the storage/ stability studies at ambient temperatures were performed
as described in Factory A.
Factory
C
Dry mixing technique was followed using edible grade
crystal salt obtained from Tuticorin in the same manner as described
for batch mixing process in Factories A and B. The only difference
was the use of 100 kg ribbon blender with a mixing time of 5 minutes.
All the test parameters described in Factory A were done here also.
Results
Factory A: The dry mixing technique was smooth and free from any problem. The iodine
fortified salt retained the colour of common salt. The pH of a 5%
aqueous solution of the fortified salt was 9.5 and the salt was free-flowing.
When samples were tested for iodine content in different laboratories,
the results obtained were same (Table 1). The field kit showed an
iodine level of 35-40 ppm and it was uniform. In the titrimetric method,
the powder salt showed a uniform iodine level of 36 ppm and the crystal
salt had 40 ppm. Road transportation, covering a distance of about
1500 km, from Tuticorin to Hyderabad did not alter the consistency
and stability of the fortified salt (Table 2). There was no loss of
iodine even after one year of storage at ambient temperatures (Table
3). The production rate per hour by the dry mixing technique was 3
tons which was the same quantity normally produced by the spray mixing
technique in this factory.
Table 1. Iodine content of iodine fortified
salt produced by dry mixing technique in Factory A.
Iodine fortified
|
Iodine content (ppm)
|
salt type |
NIN*
|
Salt Dept**
|
State Lab***
|
Powder salt: |
|
|
|
Sample 1 |
36
|
36
|
34
|
Sample 2 |
36
|
37
|
|
Sample 3 |
6
|
36
|
18
|
Crystal salt: |
|
|
|
Sample 1 |
40
|
41
|
|
Sample 2 |
41
|
39
|
|
Sample 3 |
40
|
43
|
|
* National Institute of Nutrition, Indian Council
of Medical Research, Hyderabad, India.
** Office of Assistant Salt Commissioner, Govt of India, Tuticorin,
India.
*** Chemical Testing and Analytical Laboratory, Tamil Nadu State Govt,
Guindy, Madras, India (Only sample 1, powder salt was tested).
Table 2. Effect of transportation on iodine
stability of iodine fortified salt produced by dry mixing technique
in the Factory A.
Iodine
fortified salt type |
Iodine content (ppm)
|
|
|
Initial
|
After transportation*
|
Powder salt: |
Top layer |
36
|
36
|
|
Middle layer |
36
|
36
|
|
Bottom layer |
36
|
36
|
Crystal salt: |
Top layer |
40
|
41
|
|
Middle layer |
40
|
40
|
|
Bottom layer |
40
|
41
|
* Transported in 50 kg bags from Tuticorin to Hyderabad,
India.
Factories B and C: The iodine fortified salt was free flowing and had a bright white colour
as compared to the unfortified salt. Spot tests showed an iodine level
of 30 ppm and the titrimetric method also showed the same iodine level.
The iodine distribution was uniform (30 ppm). Transportation by road
from Machilipat-nam to Hyderabad did not affect the stability and
distribution of iodine in the fortified salt. The initial iodine level
of 30 ppm was retained even after one year of storage (Table 4). The
top, middle and bottom layers of the fortified salt in the 50 kg bags
showed the same iodine concentration. The iodine content, uniformity
and stability of the fortified salt remained the same in both batch
mixing and continuous process in the Factory B. The pH of a 5% aqueous
solution of the fortified salt was 9.1 in the two factories. The production
was smooth and no problem was observed. The observed daily production
rate by the dry mixing technique was the same as with the spray mixing
technique in these two factories.
Table 3. Stability and shelf-life of iodine
fortified salt produced by dry mixing technique in the Factory A.
Iodine fortified
|
Iodine content (ppm)*
|
salt type |
Initial
|
3 mo
|
6 mo
|
9 mo
|
12 mo
|
Powder salt: |
|
|
|
|
|
Top layer |
36.0
|
35.9
|
35.8
|
36.1
|
36.1
|
Middle layer |
36.0
|
36.1
|
36.0
|
35.9
|
36.0
|
Bottom layer |
36.0
|
35.8
|
35.9
|
35.8
|
36.1
|
Crystal salt: |
|
|
|
|
|
Top layer |
40.0
|
41.0
|
41.1
|
41.2
|
41.0
|
Middle layer |
40.0
|
40.0
|
40.3
|
40.2
|
< 1000 p align="center">40.1
|
Bottom layer |
40.0
|
41.0
|
41.0
|
41.1
|
41.1
|
* Stored in 50 kg bags at ambient temperatures.
Table 4. Stability and shelf-life of iodine
fortified salt produced by dry mixing technique in the Factories B
and C.
Factory |
Iodine content (ppm)*
|
Factory B |
Initial
|
3 mo
|
6 mo
|
9 mo
|
12 mo
|
(i) Batch mixing |
|
|
|
|
|
Top layer |
30.0
|
29.9
|
30.1
|
30.0
|
30.0
|
Middle layer |
30.1
|
30.0
|
30.2
|
30.2
|
30.1
|
Bottom layer |
29.9
|
30.0
|
29.8
|
29.9
|
29.8
|
(ii) Continuous |
|
|
|
|
|
Top layer |
30.0
|
29.8
|
29.8
|
30.1
|
30.1
|
Middle layer |
30.0
|
29.8
|
29.7
|
30.0
|
30.0
|
Bottom layer |
30.0
|
29.7
|
29.8
|
30.2
|
30.1
|
Factory C |
|
|
|
|
|
Top layer |
30.0
|
30.1
|
29.9
|
30.2
|
30.1
|
Middle layer
|
30.0
|
30.1
|
30.2
|
30.1
|
30.0
|
Bottom layer |
30.1
|
30.1
|
30.0
|
29.9
|
30.0
|
* Stored in 50 kg bags at ambient temperatures.
Discussion
In the fortification of common salt with iodine, the
object is to add a predetermined, very small proportion of an iodine
compound in such a way that it is uniformly and effectively mixed
with a very much greater bulk of material (salt) to produce a homogenous
mixture which is preferably non-caking and in any case, capable of
withstanding any tendency for the constituents to segregate. Essentially,
there are three techniques to achieve this objective: spray mixing,
dry mixing and submersion processes. Continuous large-scale spraying
techniques generally involve conveyor mech-anisms and, as a rule,
are designed to treat fine, free-flowing salt. Dry mixing methods
provide for the addition of non-caking and stabilising compounds in
addition to the iodine compounds. The submersion process depends mainly
on the natural environment as it is an open field technique and has
associated quality problems.
In a tropical country like India, addition of water
to dissolve the iodine compound in the spray mixing technique, ultimately
increases the moisture of the fortified salt by an extra 2-3% which
in turn plays a detrimental role on the stability of iodine and the
shelf-life of the iodine fortified salt. In an earlier study, it was
observed that the iodine loss ranged from 25 to 30% in the first 3
months after fortification although KIO3 was used as the
source of iodine8. The justification of fixing an iodine
level of not less than 30 ppm at the production level is to allow
for loss of iodine so a minimal level for the consumer of 15 ppm would
be available.
In addition to problems due to extra moisture, the
spray mixing technique requires a reservoir for iodate solution, a
pump and an air blower to spray the solution. A dryer is also needed
to remove the extra moisture from the fortified salt whenever necessary.
Thus, the cost of the production increases in the spray mixing technique
due to the additional inputs in the form of extra machinery, electricity
and higher level of iodation, as compared to the dry mixing technique
where the spraying system is not used. These are the drawbacks observed
in the spray mixing technique. What is actually needed is an inexpensive
and comparatively simple method which can ensure uniform distribution
of iodine and satisfactory stability of iodine in the fortified salt.
The present study shows that all these factors are achievable with
the dry mixing technique in these factories. The usefulness of the
dry mixing technique for salt fortification with other nutrients,
such as iron, has been demonstrated in India9,10. The present
study confirms these observations.
Most of the salt produced in India is crystalline
salt obtained by heated open-pan or solar evaporation of brines. A
simple process by which crystalline salt can be crushed and easily
mixed with a stock mixture of KIO3 and calcium carbonate
(or magnesium carbonate 1000 ) to produce iodine fortified salt is
ideal for the country. Since the amount of carbonate added is considerably
greater than the quantity of potassium iodate, this process ensures
homogeneity and results in a very satisfactory uniformity of iodate
distribution in the fortified salt. An important advantage of KIO3
is its low solubility in water compared with the high solubility of
potassium iodide (KI). If a package of salt fortified with KI becomes
damp, the iodide is attracted to the areas of high moisture content
and then migrates from the body of the salt to the fabric of the container.
This results in a loss of iodide from the mass of the salt with a
consequent reduction of its iodine content. Because of the low solubility,
KIO3 migrates much less readily. Furthermore, the addition
of carbonate prevents this migration and hence enhances the stability
and shelf-life of the fortified salt. This benefit was observed in
the present study as there was no difference in the iodine content
of the top, middle, and bottom layers of the fortified salt after
transportation (Table 2) nor during storage (Tables 3 and 4). This
observation is also in agreement with others11. Calcium
carbonate has been found useful as an iodised salt conditioner in
the factory for the iodine fortification of crystalline salt by dry
mixing technique abroad12.
It can be seen, that in all three factories, the dry
mixing technique was successful, smooth, and economical for the large
scale production of iodine fortified salt of uniform iodine distribution
and long shelf-life. The method is patently less expensive when the
spraying system is not required in existing plants for batch mixing
or continuous processes. The carbonates used in the study are inexpensive
(about one paise per kg of salt) and their cost in the fortified salt
is offset by a reduction in the initial level of iodine to 20 ppm
instead of 30 ppm, and the expenditure on the import of iodine can
be minimised. Iodine fortification salt factories in India can readily
convert from the existing spray mixing plants to the dry mixing technique
without any additional cost and can continue to maintain the same
daily production rate of fortified salt.
The work done in M/s Sahayamatha Salterns (P) Ltd,
Tuticorin, India is based on a study by the committee of which the
authors were the members constituted by the Salt Commissioner, Government
of India, to examine the technical feasibility of iodation of salt
by the dry mixing technique in India.
Acknowledgments. The interest shown and the encouragement given by Dr Vinodini
Reddy, Director, NIN and Shri R Prakash, Salt Commissioner, Government
of India in this study are gracefully acknowledged. The authors are
extremely thankful to the owners of the factories for their unstinted
cooperation in the study. Thanks are also due to Mrs Swayamprabha
for her excellent secretarial assistance.
References
- Status Report on the National Iodine Deficiency
Disorders Control Programme (NIDDCP). Policy and Advocacy Meeting
on Iodine Deficiency Disorders (IDD), New Delhi, January 17, 1994.
- Universalisation of Access to Iodised Salt - A
Mid-decade Goal. The Salt Department, Ministry of Industry, Govt
of India, January, 1994.
- Sooch SS, Deo MG, Karmarkar MG, Kochupillai N,
Ramachandran K, Ramalingaswami V. Prevention of endemic goitre with
iodised salt. Bull WHO 1973; 49: 307-12.
- Ranganathan S, Narasinga Rao, BS. Stability of
iodine in iodised salt, Indian Food Industry 1986; 5: 1 ae4 22-124.
- Proceedings of the Motivation Campaign of IDD Control
through salt iodation: March 14, 1992, Udagamandalam, India, Salt
Dept, Government of India, Deputy Salt Commissioner, Madras, p 14.
- Narasinga Rao BS, Ranganathan S. A simple field
kit for testing iodine in salt. Food and Nutrition Bulletin 1985;
7(4): 70-72.
- AOAC. Official Methods of the Association of Official
Analytical Chemists. 15th edition. ed. K Helrich. Association of
Official Analytical Chemists Inc. Virginia, USA, 1990, p 335.
- Indian Salt Commissioner. Stability of iodine in
iodised salt. Seminar on IDD control through salt iodisation. Salt
Commissioner, Government of India, Ministry of Industry, Jaipur,
India, 1989.
- Ranganathan S. Fortification of common salt with
iron: Use of polyphosphate stabilisers. Food Chemistry. 1992; 45:
263-267.
- Ranganathan S, Dillikumar PK, Ramamoorthy P, Vinodini
Reddy. Large scale production of iron fortified salt. J Food Sci
Technol 1993; 30(3): 166-168.
- Kelly FC. Studies on the stability of iodine compounds
in iodised salt, Bull WHO 1953; 9: 228.
- Holman JCM, McCartney W. Iodised salt, In: WHO
Monograph Ser. No 44, Endemic goitre, World Health Org, Geneva,
1960; 424-426.
Dry mixing technique for the large
scale production of iodine fortified salt in India
S Ranganathan , S Sundaresan, I Raghavendra and S Kalyani
Asia Pacific Journal of Clinical Nutrition (1997) Volume 6, Number
2: 92-94
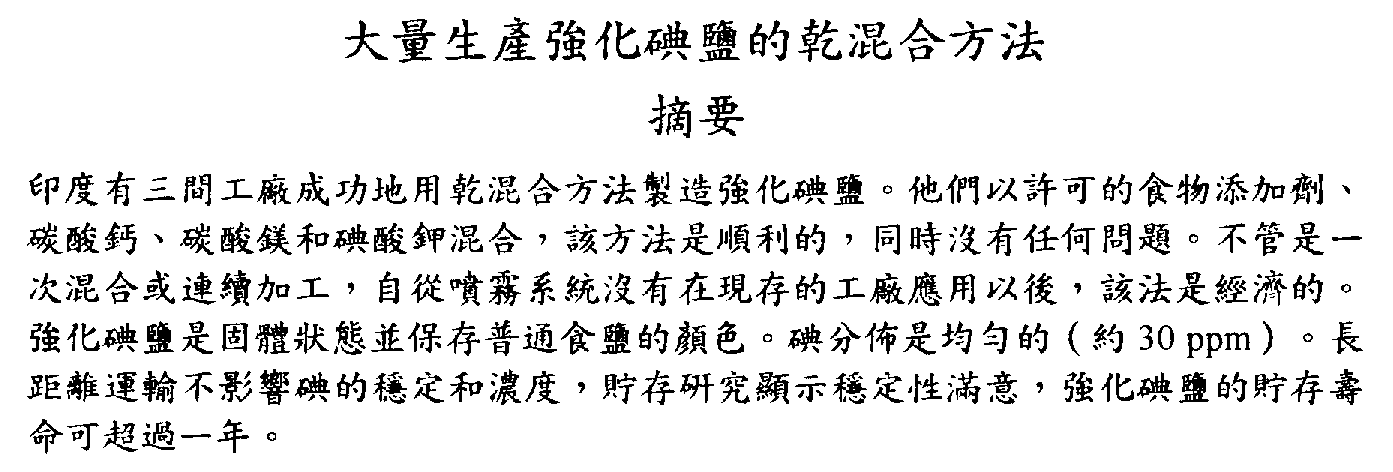

Copyright © 1997 [Asia Pacific Journal of Clinical
Nutrition]. All rights reserved.
to the top
0